What Can Squint Do For You?
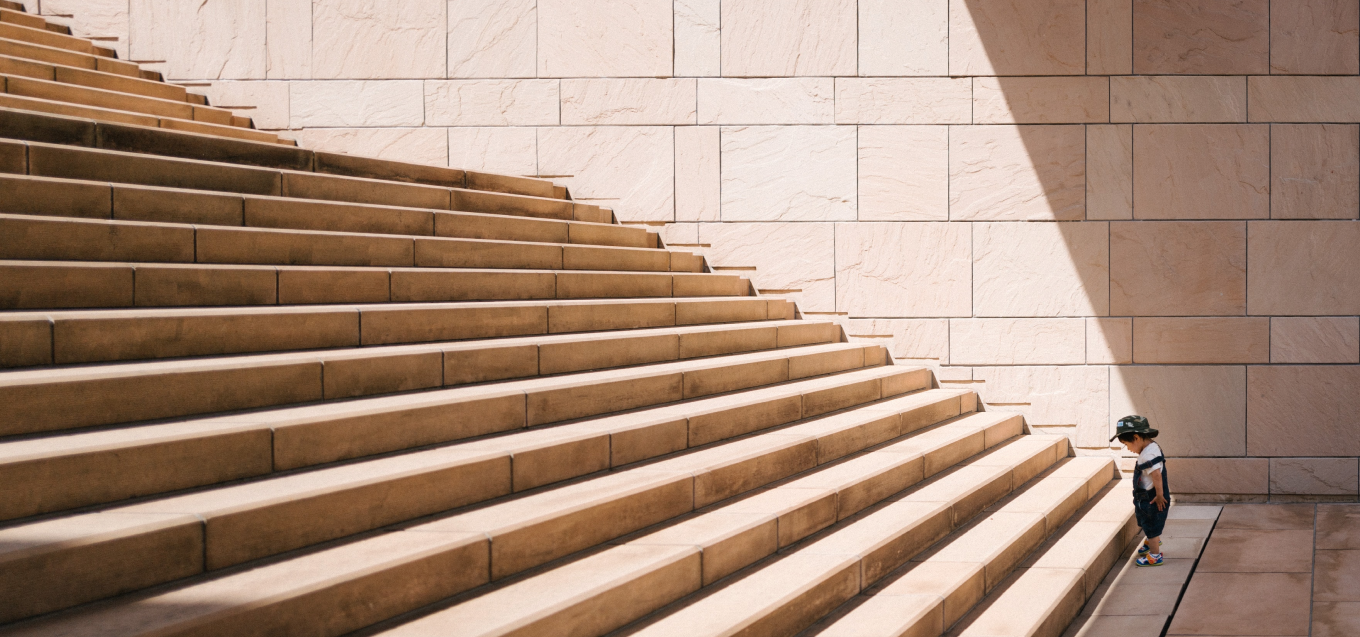
Hi, we’re Squint. The Squint team has spent hours and hours talking to industry experts, in factories, over beers, living and breathing manufacturing because Squint wants to make the best possible software to help you achieve your goals. The outcome of these many, many conversations is that we hear manufacturing problems — it’s hard to deploy new software, it's a pain to standardize SOPs, and engaging operators is a huge unsolved priority.
Squint is trying to tackle these problems to make your life easier, let’s dive in.
Challenge #1 - Setups are a Headache
“I seriously considered engraving my QR codes so that they would stop falling off the walls”
It’s really intimidating to try out new things because of the long process from training people to use the software, giving them the right tools, and finally managing the roll-out. All of this just to evaluate software before deciding whether or not to move forward. Two of the biggest challenges Squint has found in this process are the hassle of user management and then physically tagging machines with barcodes or QR codes all around a facility.
User Management & Login
One of the most challenging parts of digitizing the factory floor actually comes before the rollout of the software itself: requiring people on the floor to remember passwords and log in / out of shared tablets, phones, and computers.
Squint takes a new and unique approach to login. No more asking your workforce to remember usernames and passwords. Simply flash your company badge in front of your phone or tablet and Squint will instantly recognize and log you into your profile. Designed to be an invisible step, badge login allows you to use shared devices on the floor with ease and no unnecessary cognitive load for your users.
Physical QR Codes
If you manage to get past the login process and start seeing success in your pilot project, you’re usually looking at a lot of change management to introduce visual tags (like QR codes) to areas and machines around the floor. This can be especially challenging because physical tagging can be time-consuming, and the tags can quickly wear down with the everyday activity that goes on in a factory floor.
Squint has done away with physical tagging entirely to ensure customers experience “3 minutes from App Store to Shop Floor!”. No more QR codes and no more physical barriers to piloting or scaling your pilot. Just like login, Squint tries to make the step of retrieving information invisible. Users can simply select an area of the floor and Squint will immediately recognize it and provide the user with any existing and relevant content (operator notes, workflows, etc). Instead of tagging equipment, all you have to do with Squint is create an “Area” by spending 10 seconds pointing your camera at the area and moving around (similar to taking a panoramic photo). Squint enables this by using a variety of intelligent information captured via the device, such as: WiFi triangulation, visual object classification, and image histogram matching.
Challenge #2 - SOP Standardization & Operator Training
“It always takes me half a minute to find the e-stop”
Have you heard about the story of the magic 3-ring binder? There’s a rumor that one day, the dusty 3-ring binder that contains all of your SOPs came to life. It hopped off the shelf, and waddled all around the factory floor coming to operators to help fill gaps in instruction. It jumped up and pointed to the exact HMI, while yelling out the exact settings. On that day, the true standard operating procedure was followed to a T.
Okay, you got us - we made that story up. But, Squint does add that same magic back into your SOPs. We call that magic: Workflows.
Workflows are your SOPs digitized and magic-tized. Specifically, a workflow is a series of steps, each containing one instruction and a spatial tag (a pin that shows up through the camera and in the real world, connecting digital information to things in the real world). Since Squint runs as an app on any handheld device, it uses the device camera to see the world and show operators exactly where they need to go, look, push, and prod to complete the instruction correctly. Overall, Squint Workflows can lead operators through a procedure, audit, safety, or maintenance exercise - really anything. As we like to say: the world is your workflow!
Challenge # 3: Operator Engagement
“I’m sure you’ve heard over and over again that operator retention is a big problem.”
If operator retention challenges ring true for you, the good news is that you’re not alone. The bad news is if this rings true for you - you’ve still got a big challenge. That is, until you start using Squint.
With Squint, operators stay engaged and connected to both management and other operators. Squint enables this by allowing anyone to leave digital sticky notes that are spatially tagged around the facility and consumable asynchronously by future visitors to that physical location.
To start, this encourages operators to share feedback with plant managers about processes that are working, and about machines that aren’t. With only a few clicks, any operator can type in their targeted feedback or simply snap a pic, then their note becomes visible to others at the plant (and physically tied to a specific location) so immediate action can be taken.
Second, operators can share their tribal knowledge with each other and management! This would be the equivalent of every operator using the same personal notebook to track their learnings, meaning shared learnings can multiply amongst your operators — increasing collaboration, productivity, and, ultimately, OEE.
Finally, shift transfer is made easy because your operators can directly leave notes for each other. The operators on one shift don’t need to know who’s on the shift after them, they can simply tag a machine and add their notes. Then, when the next shift arrives they can see the shared content, read up, and start their shift informed and prepared. Practically, this means that preventative maintenance is caught faster, material waste can be curbed and operators can actively contribute to the system and feel engaged.
That's It!
Overall, operators are the heart of this industry and that is mirrored with Squint. We think it’s possible for operators to feel empowered and engaged, and this is just the beginning.