Augmented Reality in Manufacturing: Squint’s Top Insights from 2022
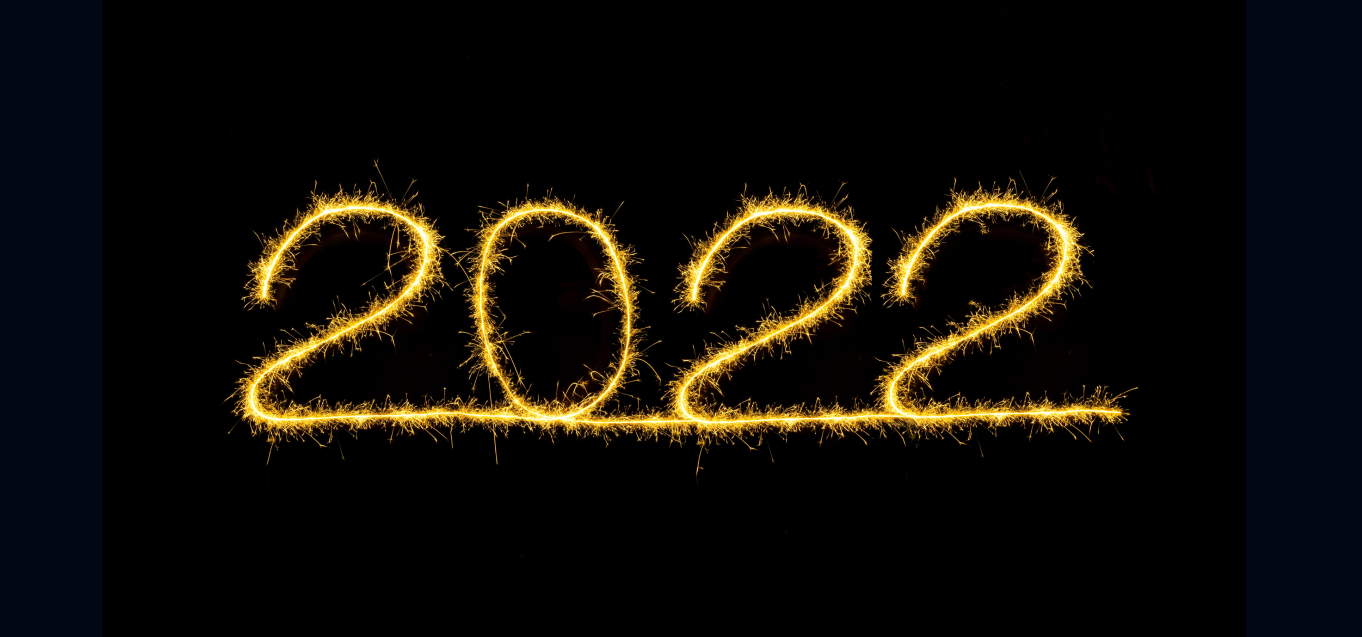
It's been a great year, filled with exciting new customer projects and features! As we reflect on the past year, the Squint team wanted to share the most common challenges we heard from users in 2022 and offer our thoughts on how to address them.
First, what’s Squint?
Squint is a powerful technology solution that leverages augmented reality (AR) to improve the efficiency and accuracy of procedures and workforces.
SOPs for operations, training, and maintenance can be digitized and enriched with spatial point-by-point guidance around any space through Squint. Squint enables users to confidently and correctly perform any procedure.
“Squint simplifies procedures by displaying the actual SOP steps in the field, making it easy for users to follow.” — Operator, Oil & Gas
“Thanks to Squint, a new employee with no previous operations experience was able to start a machine correctly in under 8 minutes, compared to the usual 2-week training period. This is revolutionizing the way we hire and train employees!” — Training Manager, Plastics Manufacturer
Squint is a robust application designed for use in the manufacturing and energy sectors. It can be easily deployed on phones or tablets and used by operators and supervisors in the field or on the floor. Now that we have some context, let's delve into some of the hot topics of 2022!
#1: Overcoming the Challenges of Digital Solution Implementation in Manufacturing
Industry Challenge
While the value of digital solutions is clear, the time and specialized knowledge needed to set them up and maintain them can be costly.
Squint Solution
Squint is quick and easy to set up, taking just a few minutes, not hours, weeks, or years. This is made possible by several unique features: first, Squint doesn't require QR codes, CAD models, or specialized cameras - you can simply use the Squint camera to map any machine, large or small, by following the instructions on the screen. Second, Squint is a mobile platform that allows you to do everything from your phone or tablet, eliminating the need to switch between applications or invest in additional devices or headsets. Finally, Squint is designed to be user-friendly for anyone, from IT professionals to experienced technicians. Whether you're a new hire or have been working at your facility for decades, you can create procedures in minutes without any special training.
“It’s like we went from Windows 95 to a brand new Macbook.” — Chief Operating Officer, Oil & Gas
“I digitized an SOP in under 3 minutes.” — Six Sigma Lead
#2: Best Practices for Efficient Training in Manufacturing with High Frontline Turnover
Industry Challenge
Another significant challenge we heard about this year is frontline turnover. The U.S. Bureau of Labor Statistics reports frontline turnover in manufacturing at 39.9% for 2021 (source). High operator turnover brings problems across the operational field.
This hits training particularly hard since programs have to train all of these new hires, some without previous experience, without compromising quality.
“Squint has been a lifesaver for training our new hires, many of whom have limited prior experience. The augmented reality procedures walk them through each step and provide all the information they need, just like a personal trainer. And even after training, Squint gives them access to on-the-job reference material to help them avoid mistakes. We’ve seen significant improvement in efficiency and performance, despite the large number of new faces on the team.” — Training Manager, Auto Manufacturing
Additionally, high frontline turnover can make it difficult to maintain accountability and capture and share tribal knowledge, which is essential for smooth operation.
Squint Solution
After discussing this challenge with our users earlier this year, the Squint team released Squint Forms – a feature that unlocks self-service training for new hires of any experience level and increases operator accountability.
To get started with Squint Forms, simply add a multiple choice selection, photo upload, number input, or short text answer to a Procedure. When the Procedure is run, operators will automatically be prompted to engage and submit data.
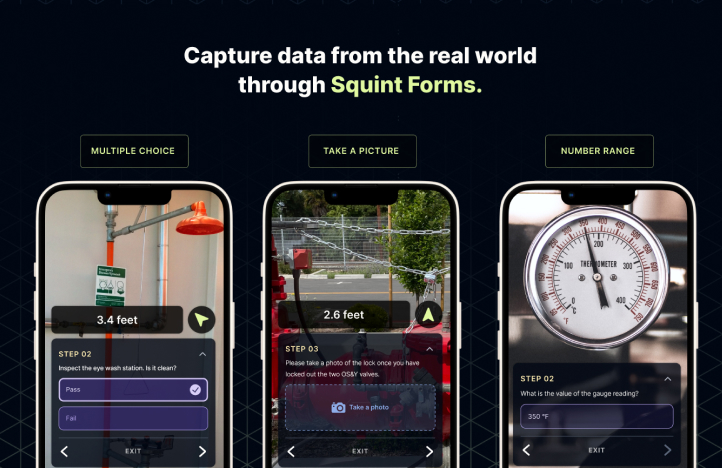
Squint customers can:
Expand training capacity...
by implementing a self-guided learning module through Squint. This allows new trainees to receive the same level of personalized instruction as if they were working with a dedicated trainer, without placing additional demands on the training staff.
Enhance accountability...
by incorporating forms into existing procedures, such as the lock-out/tag-out (LOTO) process. This will require operators to upload photos of their work, enabling supervisors to review and monitor performance over time.
Improve traceability and accountability...
by generating auditable logs during quality inspections and maintenance procedures. This will enable you to capture and analyze data about machine or process performance over time, helping you identify best practices and optimize operations.
—
In summary, Squint Forms can help your organization maintain consistent operations and performance, even with high employee turnover, by providing scalable training, promoting accountability and standardization on the factory floor, and generating comprehensive, long-term records of machines, maintenance, and production activity. This can assist supervisors in ensuring that best practices are followed and machine performance is optimized, even when operators leave the team.
That’s it!
We hope you enjoyed reading our blog post! If you're interested in learning more about how our industry knowledge and expertise can help your business thrive, we'd love to chat. Please feel free to book a meeting with us to discuss your specific goals and needs in more detail.
Before we go, we wanted to take a moment to thank our amazing customers for sharing and building with us this year. Your trust and support mean the world to us, and we look forward to continuing to work with you in the new year. Here’s to 2023!